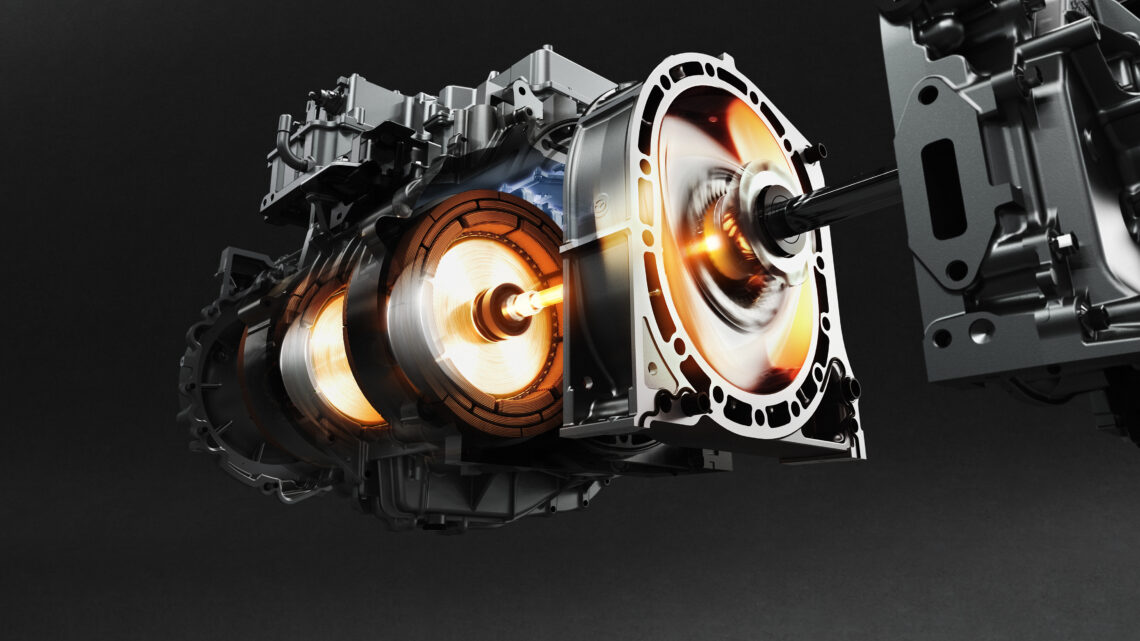
Mazda’s 8C rotatiemotor technisch bekeken
30 januari 2024Eén rotor, dus extra nauwkeurig balanceren
In een volgende productiestap worden de verspanende bewerkingen uitgevoerd, zoals het frezen van de radii, de groeven voor de zijafdichtingen en -veren, en het draaien van de gaten voor de excenteras en het tandwiel. Dit proces heeft Mazda een stuk efficiënter gemaakt, van 50 stappen bij de 13B naar negen stappen voor de 8C. De tipveren (de apex seals) op de punten van de rotor zijn bij de 8C gegroeid van 2 naar 2,5 millimeter, met het oog op een hogere betrouwbaarheid. Dan gaat de rotor naar Donphisa Processing, deze productiestap is nieuw voor Mazda. De rotor wordt in dit proces gebalanceerd, waarbij de gegevens van de 3D scan van de gietkern geverifieerd worden. De rotor wordt snel rondgedraaid waarbij de onbalans gemeten wordt, daarna wordt de rotor 3D gemeten met tastsensoren om de maatafwijkingen vast te stellen. Het feitelijke balanceren wordt uitgevoerd door kleine hoeveelheden materiaal weg te frezen, zoals ook bij het balanceren van een krukas wordt gedaan. Deze productiestap is voor de 8C erg belangrijk omdat het een enkelschijfs motor is. Bij een tweeschijfs rotatiemotor wordt de onbalans nagenoeg volledig opgeheven door de tweede rotor. Door de rotor van de 8C maximaal te balanceren hoopt Mazda de motorloop zo rustig mogelijk te krijgen. Let wel: de rotor draait niet alleen, maar hij maakt ook een oscillerende (translerende) beweging waardoor er bij een enkelschijfs rotatiemotor altijd een lichte onbalans overblijft.
Na het afwerken wordt elke rotor gebalanceerd.
Van vlakke plaat tot rotorkamer
Zoals gezegd is de maatvoering van de rotor bepalend voor de vorm van de rotorbehuizing. Deze heeft de vorm van een ingesnoerde ellips en heeft officieel ‘epitrochoïde’. Het maken van deze vorm is met enige geheimzinnigheid omgeven, en Mazda geeft niet alle geheimen prijs. Maar Mazda geeft wel openheid over het unieke productieproces, dat heel anders verloopt dat je zou verwachten. De kamer waarin de rotor draait, wordt namelijk geproduceerd uit een vlakke plaat. Deze plaat is aan één zijde in lengterichting geslepen, dat is de zijde waar de rotor draait. De achterzijde van de plaat wordt met behulp van een schaaf voorzien van meerdere groeven in de lengterichting. De plaat wordt op lengte geknipt (de lengte is precies de binnenomtrek van de rotorkamer), de einden worden aan elkaar gelast en het geheel wordt exact in de vorm van de rotorkamer gebracht. Deze beide productiestappen worden zorgvuldig afgeschermd van de buitenwereld, maar het is bijzonder om te weten dat een heel nauwkeurige, gesloten vorm uit vlakke plaat wordt gemaakt. Alsof je een cilinderbus uit plaatmateriaal maakt. De ontstane vorm wordt binnen Mazda de ‘cocon’ genoemd.
De cocon wordt gevormd uit plaatmateriaal. Hier worden de groeven in de achterzijde geschaafd.
De cocons zijn gevormd uit de vlakke plaat, nu zijn ze klaar om ingegoten te worden.